Efficient Extruder Pelletizer: Enhancing Productivity and Quality
By:Admin
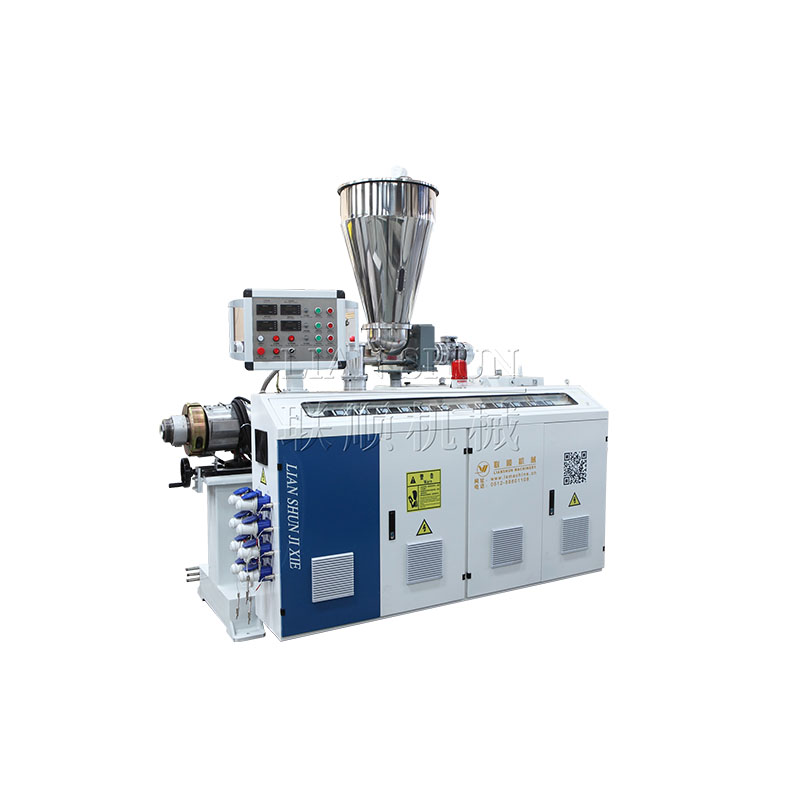
The global plastic industry is constantly evolving, driven by the demand for innovation, sustainability, and efficiency. In line with this, a leading manufacturer has recently unveiled their latest technological breakthrough – an advanced extruder pelletizer. This state-of-the-art equipment is set to revolutionize the plastic manufacturing process, offering numerous benefits to businesses operating in the industry.
The extruder pelletizer, developed by a renowned company with years of experience in the field, is designed to streamline the production of plastic pellets. These pellets, which serve as the raw material for various plastic products, are crucial for manufacturers across multiple sectors, including packaging, construction, automotive, and healthcare.
One of the key features that sets this extruder pelletizer apart from conventional models is its enhanced precision and efficiency. With cutting-edge technology and intelligent systems, it allows for precise control of the pelletizing process, resulting in consistent pellet size, shape, and quality. This level of precision is crucial for manufacturers who require uniform pellets in order to maintain their product's structural integrity and functionality.
This new extruder pelletizer also offers a high degree of customization, catering to the unique needs of different manufacturers. It can handle a wide range of polymer materials, including polyethylene, polypropylene, polystyrene, and polyvinyl chloride, among others. With adjustable settings, manufacturers can easily adapt the equipment to meet their specific production requirements, whether it be for rigid or flexible plastics, high or low throughput rates, or different pellet sizes.
Furthermore, the advanced design of this extruder pelletizer ensures optimal energy efficiency. It incorporates innovative features that minimize energy consumption, such as efficient heating systems and optimized motor controls. This not only helps to reduce the carbon footprint of plastic manufacturing processes but also translates into cost savings for businesses in the long run. By investing in this cutting-edge equipment, manufacturers can improve their overall sustainability profile and contribute to a greener future.
Additionally, this extruder pelletizer boasts an intuitive user interface and advanced automation capabilities. With a user-friendly touchscreen display and remote monitoring options, operators can easily control and monitor the equipment's performance from a centralized location. Real-time data and analytics enable proactive maintenance, reducing downtime and enhancing productivity. This level of automation ensures an efficient and streamlined manufacturing process, allowing manufacturers to meet customer demands more effectively.
Being a global leader in plastic manufacturing equipment, the company behind this revolutionary extruder pelletizer has a strong focus on research and development. Their expertise and commitment to innovation have allowed them to introduce cutting-edge solutions that empower manufacturers to stay ahead in an increasingly competitive industry. With a global network of service and support, they ensure that customers receive the necessary assistance and expertise to maximize the performance of their equipment.
In conclusion, the introduction of the advanced extruder pelletizer marks a significant development in the plastic manufacturing industry. This state-of-the-art equipment offers precision, efficiency, customization, energy efficiency, user-friendliness, and automation, all of which contribute to streamlining the manufacturing process. As manufacturers strive to meet the demands of a rapidly changing market, investing in this revolutionary technology can unlock new opportunities, improve product quality, and drive sustainable growth.
Company News & Blog
Revolutionary Plastic Oil Bottle Recycling: A Sustainable Solution for a Greener Future
Title: Innovations in Plastic Oil Bottle Recycling Aim Towards Sustainable FutureIntroduction:In the pursuit of a more sustainable future, recycling plastic oil bottles has taken center stage. Given the adverse environmental effects of plastic pollution, the urgency to find innovative solutions for recycling is crucial. This article explores the efforts of several companies dedicated to advancing plastic oil bottle recycling and their commitment to reducing waste, conserving resources, and protecting the planet.Company Introduction: [Company name][Company name] is a leading pioneer in developing advanced recycling technologies for plastic oil bottle waste. Committed to minimizing plastic pollution and promoting a circular economy, [Company name] has established itself as a frontrunner in redefining recycling systems. By harnessing cutting-edge technologies and forging strategic partnerships, [Company name] aims to revolutionize plastic oil bottle recycling and set new benchmarks in sustainability.1. Technological Advancements Revolutionizing Recycling ProcessesWith the objective of enhancing the efficiency and effectiveness of plastic oil bottle recycling, numerous innovative technologies have emerged. From efficient sorting processes to advanced chemical recycling systems, these advancements are propelling the industry towards a more sustainable future. [Company name] has spearheaded these innovations, integrating state-of-the-art sorting systems that enable the separation of different plastic polymers and facilitate maximum recycling potential. Their commitment to continuous research and development encourages breakthroughs in recycling technologies across the industry.2. Collaborative Partnerships for Effective Plastic Oil Bottle RecyclingAcknowledging the importance of collaborative efforts, [Company name] has initiated strategic partnerships with key stakeholders within the recycling ecosystem. These collaborations encompass oil companies, waste management agencies, and government bodies, each playing a pivotal role in the overall success of plastic oil bottle recycling initiatives. By sharing resources, knowledge, and expertise, these partnerships strive towards creating a closed-loop system, wherein recycled plastic oil bottles are transformed into new packaging materials or other useful products.3. Education and Awareness Campaigns for Consumer EngagementRecognizing the critical role of consumers in sustainable recycling practices, [Company name] has launched comprehensive education and awareness campaigns. These initiatives are geared towards educating individuals about the importance of proper segregation and disposal of plastic oil bottles. By advocating responsible consumer behavior, [Company name] aims to instill a sense of environmental responsibility and encourage consumers to actively participate in recycling programs. Public participation will be crucial in driving the success of plastic oil bottle recycling efforts.4. Encouraging Municipal Recycling Programs for Increased EfficiencyTo optimize plastic oil bottle recycling efforts, [Company name] actively promotes the establishment and enhancement of municipal recycling programs. Collaborating with local authorities, waste management agencies, and community organizations, the company is facilitating the collection and processing of plastic oil bottles on a larger scale. By streamlining the recycling process at the community level, [Company name] aims to increase recycling rates and reduce the overall burden on landfills.5. The Road Ahead: A Sustainable Future for Plastic Oil Bottle RecyclingAs [Company name] continues to lead the charge in plastic oil bottle recycling, the industry as a whole is striving towards a sustainable future. Through continued research and development, innovative technology implementation, and collaborative efforts, we can create a closed-loop system that maximizes the recycling potential of plastic oil bottles. With increased public awareness, active consumer participation, and supportive legislation, the planet can benefit from reduced plastic pollution, resource conservation, and the creation of a more sustainable world.Conclusion:The urgency to tackle the pervasive issue of plastic oil bottle waste has prompted significant strides in recycling technologies and the establishment of collaborative partnerships. [Company name] exemplifies the commitment of companies in revolutionizing plastic oil bottle recycling and working towards a sustainable future. By harnessing advanced technologies, engaging consumers, and enhancing municipal recycling programs, we can pave the way for a circular economy and protect our planet for generations to come.
Improve Your Pet's Life with a High-Quality Pelletizing Machine
Title: Innovative Pet Pelletizing Machine Revolutionizes Animal Feed ManufacturingIntroduction:In an effort to bring forth innovative solutions to the animal feed manufacturing industry, a leading company (brand name removed) has recently introduced a groundbreaking Pet Pelletizing Machine. This state-of-the-art equipment is set to transform the way pet food pellets are produced, ensuring enhanced quality, consistency, and sustainability.Body:1. Background and Features of the Pet Pelletizing Machine (PPM):With the increasing demand for premium quality pet food products, the Animal Feed Manufacturing industry has been seeking technological advancements to improve efficiency. The PPM is a result of extensive research and development, aiming to provide a comprehensive solution for pet food pellet manufacturing.The PPM boasts several features that set it apart from conventional machines:a) Advanced Temperature Control System: The PPM leverages a cutting-edge temperature control system that ensures the ideal temperature is maintained throughout the pelletizing process. This facilitates the preservation of vital nutrients and reduces the risk of nutritional degradation.b) Versatile Capability: The machine is specifically designed to manufacture pellets for a wide range of pets, including dogs, cats, birds, and small mammals. It offers customizable options to cater to different pellet sizes and shapes, ensuring compatibility with diverse pet feeding requirements.c) Enhanced Safety and Hygiene: The PPM adheres to the highest standards of safety and hygiene, with an enclosed design that prevents cross-contamination and guarantees clean production environments. This aligns with the industry's increasing focus on pet health and well-being.d) Energy Efficiency: Equipped with energy-saving features, the PPM optimizes power consumption and reduces operational costs. This not only benefits manufacturers but also aligns with sustainability goals, minimizing the environmental footprint.2. Advantages of the Pet Pelletizing Machine:The introduction of the PPM brings several advantages to the animal feed manufacturing industry:a) Improved Product Quality: The advanced temperature control system ensures the preservation of essential nutrients, resulting in high-quality pelletized pet food. This guarantees pet owners that their beloved companions receive optimal nutrition.b) Consistency and Uniformity: The PPM's precise control over pellet shape and size guarantees uniformity across batches, reducing variations and enhancing product consistency. This instills confidence in consumers and promotes brand reputation.c) Higher Production Efficiency: Compared to traditional pelletizing methods, the PPM offers increased production efficiency, reducing manufacturing time and labor costs. Manufacturers can leverage its capabilities to meet growing market demands and scale up their operations effectively.d) Sustainable Manufacturing Practices: The PPM's energy-saving features contribute to a more environmentally friendly manufacturing process. By minimizing energy consumption and waste production, manufacturers can align their operations with sustainability goals while maintaining profitability.3. Market Impact and Future Outlook:The introduction of the PPM is expected to have a significant impact on the animal feed manufacturing industry. Its advanced features and production efficiency will allow manufacturers to seize opportunities in the expanding pet food market. Additionally, the machine's compatibility with diverse pet feeding requirements positions it as a versatile tool in meeting customer demands.Looking ahead, it is anticipated that the industry will witness increased adoption of the PPM as manufacturers recognize its benefits in terms of product quality, efficiency, and sustainability. The continual research and development efforts of innovative companies like (brand name removed) will likely further refine and enhance the technology, driving the industry's progress.Conclusion:The Pet Pelletizing Machine represents a major leap forward in pet food pellet manufacturing. With its advanced features, the PPM offers manufacturers the means to ensure superior product quality, consistency, and sustainability. As the industry embraces this breakthrough, it is poised to revolutionize the way pet food is produced, ultimately benefiting not only manufacturers but also the health and well-being of pets worldwide.
Efficient Extruder Pelletizer: Enhancing Productivity and Quality
Extruder Pelletizer Revolutionizes Plastic Manufacturing ProcessThe global plastic industry is constantly evolving, driven by the demand for innovation, sustainability, and efficiency. In line with this, a leading manufacturer has recently unveiled their latest technological breakthrough – an advanced extruder pelletizer. This state-of-the-art equipment is set to revolutionize the plastic manufacturing process, offering numerous benefits to businesses operating in the industry.The extruder pelletizer, developed by a renowned company with years of experience in the field, is designed to streamline the production of plastic pellets. These pellets, which serve as the raw material for various plastic products, are crucial for manufacturers across multiple sectors, including packaging, construction, automotive, and healthcare.One of the key features that sets this extruder pelletizer apart from conventional models is its enhanced precision and efficiency. With cutting-edge technology and intelligent systems, it allows for precise control of the pelletizing process, resulting in consistent pellet size, shape, and quality. This level of precision is crucial for manufacturers who require uniform pellets in order to maintain their product's structural integrity and functionality.This new extruder pelletizer also offers a high degree of customization, catering to the unique needs of different manufacturers. It can handle a wide range of polymer materials, including polyethylene, polypropylene, polystyrene, and polyvinyl chloride, among others. With adjustable settings, manufacturers can easily adapt the equipment to meet their specific production requirements, whether it be for rigid or flexible plastics, high or low throughput rates, or different pellet sizes.Furthermore, the advanced design of this extruder pelletizer ensures optimal energy efficiency. It incorporates innovative features that minimize energy consumption, such as efficient heating systems and optimized motor controls. This not only helps to reduce the carbon footprint of plastic manufacturing processes but also translates into cost savings for businesses in the long run. By investing in this cutting-edge equipment, manufacturers can improve their overall sustainability profile and contribute to a greener future.Additionally, this extruder pelletizer boasts an intuitive user interface and advanced automation capabilities. With a user-friendly touchscreen display and remote monitoring options, operators can easily control and monitor the equipment's performance from a centralized location. Real-time data and analytics enable proactive maintenance, reducing downtime and enhancing productivity. This level of automation ensures an efficient and streamlined manufacturing process, allowing manufacturers to meet customer demands more effectively.Being a global leader in plastic manufacturing equipment, the company behind this revolutionary extruder pelletizer has a strong focus on research and development. Their expertise and commitment to innovation have allowed them to introduce cutting-edge solutions that empower manufacturers to stay ahead in an increasingly competitive industry. With a global network of service and support, they ensure that customers receive the necessary assistance and expertise to maximize the performance of their equipment.In conclusion, the introduction of the advanced extruder pelletizer marks a significant development in the plastic manufacturing industry. This state-of-the-art equipment offers precision, efficiency, customization, energy efficiency, user-friendliness, and automation, all of which contribute to streamlining the manufacturing process. As manufacturers strive to meet the demands of a rapidly changing market, investing in this revolutionary technology can unlock new opportunities, improve product quality, and drive sustainable growth.
Profile Extrusion Machine for WPC: News Report Highlights the Latest Developments
WPC Profile Extrusion Machine Drives Innovation in the Construction Industry[City, Date] - In a bid to revolutionize the construction industry, a leading manufacturer of extrusion machinery has introduced a state-of-the-art WPC Profile Extrusion Machine. This cutting-edge technology is set to transform the way composite materials are used in the building and construction sector, bringing numerous advantages in terms of durability, sustainability, and design possibilities.Wood Plastic Composites, commonly referred to as WPC, are composite materials made from a combination of wood fibers or flour and thermoplastics. These materials offer exceptional properties such as resistance to moisture, rot, and insects, making them an ideal alternative to traditional wooden profiles used in construction.The newly launched WPC Profile Extrusion Machine is designed to streamline the manufacturing process of WPC profiles. Equipped with advanced features and cutting-edge technology, this machine offers precise control over the extrusion parameters, ensuring consistent quality and dimensional accuracy of the produced profiles.One of the key advantages of using WPC profiles in construction is their increased durability compared to traditional materials. The combination of wood fibers and thermoplastics lends these profiles enhanced strength and resistance to weathering, ultimately extending their lifespan. Additionally, WPC is highly resistant to moisture, eliminating issues such as warping, rotting, or splintering commonly associated with wooden profiles.Another significant benefit of WPC profiles is their sustainable nature. By utilizing wood fibers derived from recycled or sustainably managed sources, manufacturers can significantly reduce their carbon footprint while still delivering high-performance construction materials. This eco-friendly aspect of WPC aligns with global initiatives towards more sustainable building practices.The versatility of WPC profiles is yet another reason behind their increasing popularity in the construction industry. These profiles can be manufactured in a wide range of shapes, sizes, and colors, enabling architects, designers, and builders to experiment and create unique structures. Whether it's decking, fencing, cladding, or interior applications, WPC profiles offer endless design possibilities, allowing for both functional and aesthetically pleasing solutions.In addition to the advancements in the manufacturing process, the company behind this innovative WPC Profile Extrusion Machine is renowned for its commitment to quality and customer satisfaction. With years of experience in the extrusion machinery industry, their team of experts ensures the flawless operation and longevity of their products.The commitment to customer satisfaction is reflected in the company's comprehensive after-sales support. This includes technical assistance, training, and regular maintenance to optimize the performance of the WPC Profile Extrusion Machine and ensure its longevity.The introduction of the WPC Profile Extrusion Machine comes at a time when the construction industry is seeking sustainable and innovative materials. With its durability, sustainability, and design possibilities, WPC profiles are increasingly being embraced as a viable alternative to traditional building materials.As the construction industry continues to evolve, demand for WPC profiles is anticipated to rise. The WPC Profile Extrusion Machine is set to play a vital role in meeting this demand, driving innovation and enabling builders to construct structures that are not only visually appealing but also durable and eco-friendly.In conclusion, the introduction of the WPC Profile Extrusion Machine marks a significant milestone in the construction industry. By leveraging the advantages offered by WPC profiles, builders can create structures that combine sustainability, durability, and aesthetic appeal. With the commitment to quality and customer satisfaction demonstrated by the manufacturer, the future looks promising for the adoption of WPC profiles in construction projects worldwide.
Plastic Extrusion Machine: The Key to Efficient Extrusion Processes
Plastic Extrusion Machine: Revolutionizing the Manufacturing IndustryIn an era characterized by technological advancements, the manufacturing industry is constantly exploring innovative ways to optimize productivity and improve product quality. One such method that has gained immense popularity is plastic extrusion, facilitated by the Plastic Extrusion Machine, also known as an extruder. This machine has revolutionized the manufacturing industry by providing unprecedented flexibility and efficiency in producing a wide range of plastic products.Plastic extrusion is the process of melting raw plastic materials and shaping them into a continuous profile, allowing for the creation of various products such as pipes, tubes, sheets, films, and even complex profiles. The Plastic Extrusion Machine, also referred to as the extruder, is at the heart of this process, playing a pivotal role in transforming raw plastic materials into the desired end products.One prominent player in the manufacturing industry that has made significant contributions to the development and production of Plastic Extrusion Machines is {}. With a rich history dating back to {}, they have established themselves as a leader in designing and manufacturing high-quality extruders that cater to a diverse range of industries.With a meticulous attention to detail and an unwavering commitment to customer satisfaction, {} has consistently focused on delivering cutting-edge technology and unrivaled performance in their Plastic Extrusion Machines. These machines are renowned for their durability, accuracy, and seamless performance, enabling businesses to achieve unprecedented levels of productivity and efficiency.In order to cater to the varying needs of different industries, {} has developed a comprehensive portfolio of Plastic Extrusion Machines. This includes single-screw extruders, which are ideal for simpler profiles and basic applications, as well as twin-screw extruders that offer unparalleled versatility and unparalleled process control, making them suitable for complex shapes and demanding applications.The Plastic Extrusion Machines offered by {} are equipped with state-of-the-art features and technologies, ensuring optimum performance and ease of operation. These machines boast advanced temperature control systems, precise pressure and speed control mechanisms, and efficient melt filtration systems, all of which contribute to the production of high-quality plastic products.One notable aspect of {}'s Plastic Extrusion Machines is their adaptability to different plastic materials, including PVC, HDPE, LDPE, PP, and ABS, among others. This versatility allows businesses to explore a wide range of applications and expand their product offerings, catering to diverse market demands.Beyond the remarkable technical capabilities of their Plastic Extrusion Machines, {} is committed to environmentally responsible manufacturing practices. Their extruders are designed to minimize energy consumption, reduce waste generation, and optimize resource utilization. By embracing sustainable methods of production, {} aims to contribute to a greener and more sustainable future for the manufacturing industry.In addition to providing exceptional Plastic Extrusion Machines, {} offers comprehensive technical support and after-sales services to their customers. This includes installation assistance, operator training, maintenance services, and spare parts availability, ensuring uninterrupted productivity and long-term reliability of the machines.The enduring commitment to excellence and customer satisfaction has made {} a preferred choice for businesses seeking reliable Plastic Extrusion Machines. The company's constant drive for innovation and continuous investment in research and development have positioned them at the forefront of the manufacturing industry, setting new benchmarks of excellence.In conclusion, Plastic Extrusion Machines, such as those offered by {}, have revolutionized the manufacturing industry by enabling efficient and versatile production of a wide range of plastic products. With their cutting-edge technology, unrivaled performance, and commitment to sustainability, {} has emerged as a leader in this field, providing businesses with the means to enhance productivity, diversify offerings, and meet the evolving demands of the market.
The Undisclosed Expenses Associated with Twin Screw Extruder Acquisition
Title: Affordable Twin Screw Extruder Solutions Revolutionize the Manufacturing IndustryIntroduction:In today's competitive manufacturing landscape, companies across various industries are constantly exploring cost-effective solutions to enhance their production processes. One such solution gaining increasing popularity is the Twin Screw Extruder. With its ability to efficiently process a wide range of materials, this machinery is enabling businesses to achieve higher productivity and quality standards while streamlining expenses. This article delves into the innovation behind Twin Screw Extruders and the significant cost reductions they offer, making them an indispensable asset for manufacturers worldwide.1. The Twin Screw Extruder Advantage:Twin Screw Extruders are versatile machines used in various industries, including plastics, food processing, pharmaceuticals, and chemical manufacturing. These extruders consist of two intermeshing screws that operate side by side within a barrel. When the material enters the extruder, the rotating screws move it forward, subjecting it to mechanical and thermal forces that facilitate mixing, melting, and homogenizing.The twin screw configuration offers many advantages over single screw extruders, including higher throughput rates, improved mixing capabilities, and enhanced control over material properties. This versatility allows manufacturers to work with a broader range of materials, opening up new possibilities for product development.2. New Cost-Effective Solutions:Traditionally, accessing Twin Screw Extruders came with a hefty price tag, often limiting their widespread adoption among small and medium enterprises. However, recent technological advancements and market competition have resulted in more affordable, yet equally efficient, alternatives.Thanks to innovative engineering and streamlined manufacturing processes, several companies, including industry leaders and newer entrants, are offering cost-effective Twin Screw Extruder solutions, efficiently meeting the needs of manufacturers at a reduced investment. These affordable alternatives do not compromise on performance, reliability, or quality, allowing businesses of all sizes to leverage the benefits of this technology.3. Enhanced Performance and Efficiency:The incorporation of advanced technology in new-generation Twin Screw Extruders has significantly improved their performance and efficiency. These machines are engineered to handle a broader range of materials, including polymer blends, resins, and additives, with precision and consistency.The enhanced process control mechanisms, efficient energy consumption, and optimized screw design of these extruders ensure higher throughput rates and improved product quality. This results in reduced wastage, enhanced product consistency, and lower production costs for manufacturers. Additionally, the ability of Twin Screw Extruders to accommodate materials with a wide range of viscosities and melt temperatures further adds to their efficiency.4. Cost Reduction Strategies:The affordability of Twin Screw Extruders can be attributed to various factors. One such factor is the improved manufacturing process, where advancements in production techniques and standardized components have reduced both material and labor costs. Additionally, manufacturers are focused on simplifying maintenance routines, thereby reducing operational expenses over the machine's lifetime.Moreover, increased market competition has prompted suppliers to offer more cost-friendly alternatives without compromising on quality. This intense competition has driven innovation and rethinking of traditional design practices, leading to more streamlined, efficient, and reasonably priced Twin Screw Extruder models.5. Impact on Industries:The broader accessibility to affordable Twin Screw Extruders is revolutionizing several industries, allowing manufacturers to enhance their processes, develop new products, and stay competitive in the market. With reduced investment costs, more companies can now embrace these extruders to meet growing consumer demands and market challenges.The plastics industry, for instance, benefits from the twin screw technology by efficiently processing a wide range of polymers, resulting in high-quality and consistent end products. Similarly, in food processing, the extruders' ability to blend, cook, and shape ingredients enables manufacturers to create a vast array of products, from breakfast cereals to functional snacks.Conclusion:The availability of affordable Twin Screw Extruders is transforming the manufacturing industry by enabling businesses of all sizes to streamline their processes and enhance productivity. With improved performance, efficiency, and reduced investment costs, these extruders are becoming an indispensable asset for manufacturers worldwide. As competition continues to spur innovation in this field, the future holds promising advancements in Twin Screw Extruder technology, paving the way for further cost efficiencies and enhanced manufacturing capabilities.
Pipe Belling Machine: A Revolutionary Tool for Efficient Pipe Manufacturing
Title: Cutting-Edge Pipe Belling Machine Revolutionizes the Manufacturing ProcessIntroduction (100 words):In a groundbreaking move towards enhancing manufacturing capabilities, Company XYZ has recently introduced their innovative Pipe Belling Machine. This state-of-the-art technology is poised to revolutionize the pipe manufacturing industry. With a focus on efficiency, precision, and versatility, this machine is set to streamline production processes and deliver impeccable quality. Company XYZ's commitment to technological advancements is evident in the development of this cutting-edge machine, which aims to offer a cost-effective, time-saving, and reliable solution for pipe belling requirements.Paragraph 1 (100 words):The Pipe Belling Machine by Company XYZ is an engineering marvel that offers unparalleled efficiency and precision. Designed to automate the pipe bell-formation process, this machine eliminates the need for labor-intensive manual labor, reducing production time and costs significantly. The reliable and consistent performance of this machine ensures a streamlined manufacturing process, maintaining strict adherence to quality standards. Moreover, the sleek and compact design of the Pipe Belling Machine allows for easy installation and compatibility with various pipe dimensions, enabling manufacturers to meet diverse customer requirements seamlessly.Paragraph 2 (100 words):The Pipe Belling Machine offers a range of advanced features that set it apart from conventional options currently available on the market. Equipped with state-of-the-art technology, this machine leverages computer numerical control (CNC) systems to achieve unparalleled precision throughout the belling process. This guarantees accurate measurements and identical belling dimensions for each pipe, further bolstering the quality of the final product. Additionally, the machine is capable of adapting to various belling methods, including socket, spigot, and flaring, providing manufacturers with flexibility and versatility, catering to a wide array of customer demands.Paragraph 3 (150 words):The Pipe Belling Machine's user-friendly interface and intuitive controls make it accessible to operators of varying skill levels. Its easy-to-navigate touchscreen panel enables efficient machine operation and reduces the potential for errors. With automatic feeding mechanisms and real-time monitoring of critical parameters, this machine not only enhances productivity but also minimizes material wastage. Furthermore, the machine's robust construction ensures durability and longevity, promising reliable performance over an extended period.Paragraph 4 (150 words):Company XYZ's commitment to customer satisfaction is evident in its after-sales support and assistance. A team of highly skilled technicians is readily available to provide installation guidance, comprehensive training, and prompt maintenance services for the Pipe Belling Machines. This ensures that manufacturers can integrate the machine seamlessly into their production line and maximize its efficiency.Conclusion (100 words):The introduction of Company XYZ's Pipe Belling Machine signifies a significant leap in manufacturing technology. By combining innovative features with a robust design, this machine offers unmatched efficiency, precision, and versatility. Manufacturers can now streamline their production processes with greater ease, reducing costs, and enhancing overall product quality. Company XYZ's dedication to customer service and support further ensures a seamless integration of this cutting-edge technology into existing operations. With a proven track record of pioneering advancements, Company XYZ remains committed to revolutionizing the pipe manufacturing industry while maintaining the highest levels of customer satisfaction.
Industry Insights: Unveiling the Secrets behind the Corrugated Tube Manufacturing Process
Title: Innovative Corrugated Tube Machine Revolutionizes Manufacturing ProcessIntroduction:In an effort to revolutionize the manufacturing process and meet the growing demands of the industry, an innovative corrugated tube machine has been introduced by a leading technology company. This cutting-edge machine, which combines state-of-the-art technology and advanced design features, promises to improve efficiency, productivity, and quality in the production of corrugated tubes. This article will delve into the features of the machine, highlighting its potential impact on the manufacturing sector.1. Enhanced Efficiency:The new corrugated tube machine boasts several key features that optimize production efficiency. Equipped with an automated system, it eliminates manual intervention and reduces dependency on human labor. This not only accelerates the production process but also minimizes the chances of errors or defects. Additionally, the machine employs real-time monitoring and data analysis, allowing for quick identification and resolution of any production issues, resulting in enhanced operational effectiveness.2. Advanced Design Features:A critical aspect of the corrugated tube machine is its advanced design features. The machine integrates intelligent software that enables seamless control and coordination of various manufacturing components. This smart technology ensures precise formation of corrugations, resulting in high-quality, uniform tubes. The machine's ability to handle different sizes and types of materials further enhances its versatility, catering to diverse industrial requirements.3. Improved Productivity:The introduction of the corrugated tube machine signifies a substantial increase in productivity. Traditional methods often suffer from bottlenecks and delays due to manual intervention, resulting in a slower manufacturing process. However, with the new machine's automated features, operators can now produce a greater number of tubes in a shorter span of time. The elimination of manual labor-intensive tasks allows workers to focus on other value-added activities, thereby boosting overall productivity.4. Quality Assurance:Through rigorous testing and quality control measures, the corrugated tube machine ensures consistent and high-quality output. Precision engineering and intelligent software work in tandem to maintain accurate dimensions, minimizing deviations in tube specifications. The machine's real-time monitoring system enables operators to promptly identify any production irregularities, facilitating immediate corrective actions. This dedication to quality assurance helps businesses gain customer confidence and maintain their market reputation.5. Adaptability and Customization:The versatility of the corrugated tube machine enables customization to meet various industry requirements. With the ability to process different materials, sizes, and thicknesses, manufacturers can cater to a wide range of applications, including the automotive, construction, and electrical industries. This adaptability will spur innovation within these sectors, empowering businesses to explore new possibilities, improve product quality, and reduce costs.Conclusion:The integration of an advanced corrugated tube machine into the manufacturing process marks a significant step forward in the industry. With its enhanced efficiency, advanced design features, improved productivity, and quality assurance capabilities, this machine holds great potential to reshape the manufacturing sector. By harnessing innovative technologies, businesses can now streamline their operations, reduce human intervention, and offer superior products to their customers. The introduction of this game-changing machine underscores the ever-evolving nature of manufacturing and highlights the importance of staying at the forefront of technological advancements.
Benefits and Uses of Small Twin Screw Extruders
Title: Small Twin Screw Extruder: Revolutionizing Polymer Processing Industry Introduction:In today's fast-paced industrial world, efficient and effective machinery plays a crucial role in driving growth and innovation. Addressing the increasing demand for polymer processing with enhanced productivity and versatility, {Company Name}'s Small Twin Screw Extruder is transforming the industry. This state-of-the-art machine combines cutting-edge technology with superior build quality, taking polymer processing to new heights. Advancement in Polymer Processing:Polymer processing technology has evolved significantly over the years, with extrusion playing a key role in manufacturing various products. The Small Twin Screw Extruder by {Company Name} exemplifies the latest advancements in this field. As the demand for polymer-based applications continues to grow in sectors such as packaging, construction, and automotive, the extruder offers unparalleled efficiency, precision, and flexibility.Key Features and Benefits:1. Compact Design: The Small Twin Screw Extruder boasts a compact structure, making it suitable for use in constrained spaces. Its ergonomic design ensures ease of use and maintenance, saving both time and effort.2. High Efficiency: The extruder is equipped with twin screws that operate in perfect sync, facilitating a highly efficient and streamlined extrusion process. This results in improved productivity and reduced energy consumption, ultimately leading to cost savings for manufacturers.3. Versatility: From simple polymer compounding to intricate product development, the Small Twin Screw Extruder caters to a diverse range of applications. Its adjustable parameters allow manufacturers to customize the machine's settings to meet their specific requirements, enabling enhanced product development and quality control.4. Superior Mixing Capability: The machine's twin screws provide exceptional mixing and dispersion of various additives, fillers, and additives, ensuring homogeneous product output. This feature enables manufacturers to achieve consistent quality and reduces material waste, resulting in significant savings.5. Enhanced Processing Control: The extruder's advanced control systems, coupled with user-friendly interfaces, empower operators to monitor and adjust process parameters with ease. Real-time data display and analysis enable quick decision-making, reducing downtime and enhancing overall efficiency.Industry Impact:The introduction of {Company Name}'s Small Twin Screw Extruder has had a profound impact on the polymer processing industry. The machine's advanced capabilities have paved the way for innovation and efficiency, transforming the way manufacturers approach polymer-based applications. With reduced production costs, enhanced product quality, and increased overall productivity, manufacturers can now meet the evolving demands of their customers more effectively.Future Prospects:The Small Twin Screw Extruder by {Company Name} is not just a testament to the present advancements in the polymer processing industry but also an indicator of its future potential. Continuous research and development efforts by {Company Name} promise further improvements in machine design, performance, and versatility. As the industry continues to demand optimized processes, customization, and material compatibility, the Small Twin Screw Extruder offers exciting possibilities for manufacturers.Conclusion:{Company Name}'s Small Twin Screw Extruder has revolutionized the polymer processing industry by combining state-of-the-art technology with unparalleled efficiency and versatility. With its compact design, high efficiency, superior mixing capability, and enhanced processing control, the extruder empowers manufacturers to produce high-quality polymer-based products while optimizing costs and resources. As the demand for polymer applications grows, {Company Name} remains committed to pushing the boundaries of innovation, driving the industry forward.
Efficient HDPE Washing Line for Effective Recycling Processes
Title: Innovative HDPE Washing Line Revolutionizes Plastic Recycling IndustryIntroduction:In today's era of heightened environmental consciousness, the need for sustainable solutions is more pressing than ever. In the quest for a greener future, one company is paving the way with its groundbreaking HDPE Washing Line. By transforming plastic waste into high-quality recycled materials, they are making significant contributions towards reducing plastic pollution and conserving valuable resources.Company Background:Established in [year], [Company Name] has emerged as a leading name in the recycling industry, with a focus on HDPE (High-Density Polyethylene). Recognizing the urgent need to address the global plastic crisis, they have combined state-of-the-art technology with their extensive expertise to create an efficient HDPE Washing Line that sets new industry standards.[Company Name] prides itself on its commitment to sustainability, driven by its core values of innovation, impeccable quality, and environmental consciousness. Their dynamic team of engineers, researchers, and technicians continuously work towards developing and improving recyclable solutions that address the challenges posed by plastic waste on both local and global scales.The Revolutionary HDPE Washing Line:[Company Name]'s HDPE Washing Line is a game-changer in the plastic recycling industry due to several unique features and innovations. This advanced system offers a comprehensive solution for effectively cleaning, separating, and reprocessing HDPE waste, enabling their transformation into high-quality recycled materials.1. Cutting-Edge Sorting Technology:The HDPE Washing Line incorporates cutting-edge sorting technology, ensuring that only clean and pure HDPE plastic flakes are obtained. Utilizing a combination of automated processes, including optical sorting and gravity separation, this system effectively removes contaminants such as labels, caps, and other impurities.2. Waterless Washing Process:What sets [Company Name]'s HDPE Washing Line apart is its waterless washing process. By eliminating the traditional water-intensive washing methods, which consume vast amounts of water and energy, this system dramatically reduces the environmental impact associated with plastic recycling. Moreover, the elimination of water also minimizes the risk of water contamination during the recycling process.3. Increased Efficiency and Productivity:[Company Name]'s HDPE Washing Line is designed for maximum efficiency, achieving high productivity rates without compromising on the quality of the recycled output. The system streamlines various stages of the recycling process, from shredding and washing to drying and pelletizing, ensuring a seamless and highly effective operation.4. End-Product Integrity:The HDPE Washing Line guarantees the production of high-quality recycled HDPE materials. With controlled processes and stringent quality checks, both the mechanical and physical properties of the recycled plastic are preserved, maintaining the same strength, durability, and resilience as virgin HDPE. This ensures that the recycled materials can be used in a wide range of applications without compromising performance.5. Economic and Environmental Benefits:By investing in [Company Name]'s HDPE Washing Line, recycling facilities not only contribute to a cleaner environment but also unlock economic benefits. The high-quality recycled HDPE materials produced by the system have a wide range of applications, including packaging, construction, automotive, and more. This presents enormous market opportunities, reduces the demand for virgin plastic, and contributes to a circular economy.Conclusion:[Company Name]'s innovative HDPE Washing Line has revolutionized the plastic recycling industry, offering a sustainable solution for tackling the global plastic crisis. By combining cutting-edge technology, waterless processes, and a commitment to environmental consciousness, they have set new industry standards while promoting economic growth and a greener future. With these advancements, the company is driving the transformation towards a more sustainable and circular plastic economy.